|  | 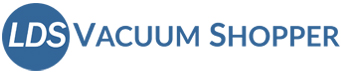

Condition Of Parts To Be Tested - Because helium leak detectors use vacuum technology as part of the testing process, it is important for wheels to be free of moisture or trapped water. It is recommended for testing to take place after the painting process. Wheels should be leak tested at an elevated temperature of at least twenty (20) degrees F above the ambient factory temperature for the best results.
All wheels exposed to water bubble tests should never be placed in the mass spectrometer without first removing the water by baking the wheels at an elevated temperature sufficient to drive off water vapor.
Cast wheels have the possibility of an extremely long leak path and hole sizes of .5 microns in diameter or smaller. If the wheel has been exposed to water prior to the helium test, blockage of the leak is a real possibility. Correlation between helium and water bubble tests is not practical because operator judgment, bubble size and frequency are not easily measured without a large uncertainty factor.
Most water bubble testers test in the opposite direction of helium detectors.
Recovery From Gross Leaks - The system must be designed to recover from gross leaks without the need for purging the pumps. Only helium stable mechanical pumps should be used in wheel leak testing applications.
Using gas mixes other than 100% helium - When using gas mixtures, it may be necessary to experiment with both pressure and concentration to accomplish the necessary results depending upon specification. The LDS helium leak testing equipment must be designed to handle a variety of gas filling concepts to allow for flexibility in this area.
Maximum recommended range of wheel sizes to be tested on a single machine - The helium leak test method will accommodate wheel sizes from 13"x4" up to 15"x7". For information on additional sizes 18"x10" or larger, see bulletin W-1.
Sealing Technology - Special urethane seals offering longer wear and positive sealing are of prime importance. Special urethane compounds are processed using a high vacuum technique to eliminate trapped gas. The sealing plate design must eliminate helium leaking under the seal assembly.
This special urethane compound and processing eliminate helium permeation and absorption into the material. Contact LDS for more information on this process.
Helium Wheel Testing Series... Bulletin W-2 © All Rights Reserved
|
Contact LDS Vacuum with any questions:
Phone (407)862-4643 via Fax (407)862-8723 or
info@ldsvacuum.com
LDS Vacuum Products is a 100% woman owned company and certified Woman Owned Small Business (WOSB) The logos and/or trademarks appearing on this page are not owned by or registered to LDS but, rather, designate products sold by LDS, and are owned and/or registered to the manufacturers or suppliers of the products.
Images Shown May Be For Reference Only
There is a global helium shortage. Each time an MRI is performed, helium is used. Please rethink your helium balloon purchase. |
|